In the world of hospitality, creating the right ambiance can make all the difference in turning an ordinary experience into an unforgettable one. And at Xi'an W Hotel, that's exactly what we did to design and craft custom lighting fixtures that perfectly captured the hotel's unique personality and style. From the lobby to the banquet hall, we transformed the hotel's interior into a breathtaking visual spectacle that dazzles guests and sets the standard for luxury accommodations in the city.
In this article, we'll shed some light on the art of custom lighting and take you behind the scenes of our collaboration with Xi'an W Hotel, revealing the secrets and techniques that went into creating some of the most stunning lighting fixtures in the hospitality industry. Whether you're a hotelier looking to elevate your guests' experience or a design enthusiast curious about the latest trends in custom lighting, this article has something for everyone.
Project Introduction:
The largest W hotel in Asia, lasted for ONE year August 20, 2017 - August 20, 2018
As a supplier of Crystal Light Fixtures for the lobby, grand banquet hall, small banquet hall of the W Hotel, We will reveal the technology behind the gorgeous products.
1 Lobby
The interior of the An W Hotel in Xian spans over 100,000 square meters, and its lobby alone boasts a 20-meter-high, 30-meter-high plane space.
The lighting solution, designed with the concept of the Milky Way galaxy, aims to embody the feeling of the vast expanse of stars while being able to rotate and programmed for RGBW dimming. After numerous discussions and intensive design upgrades, we have produced the following renderings.
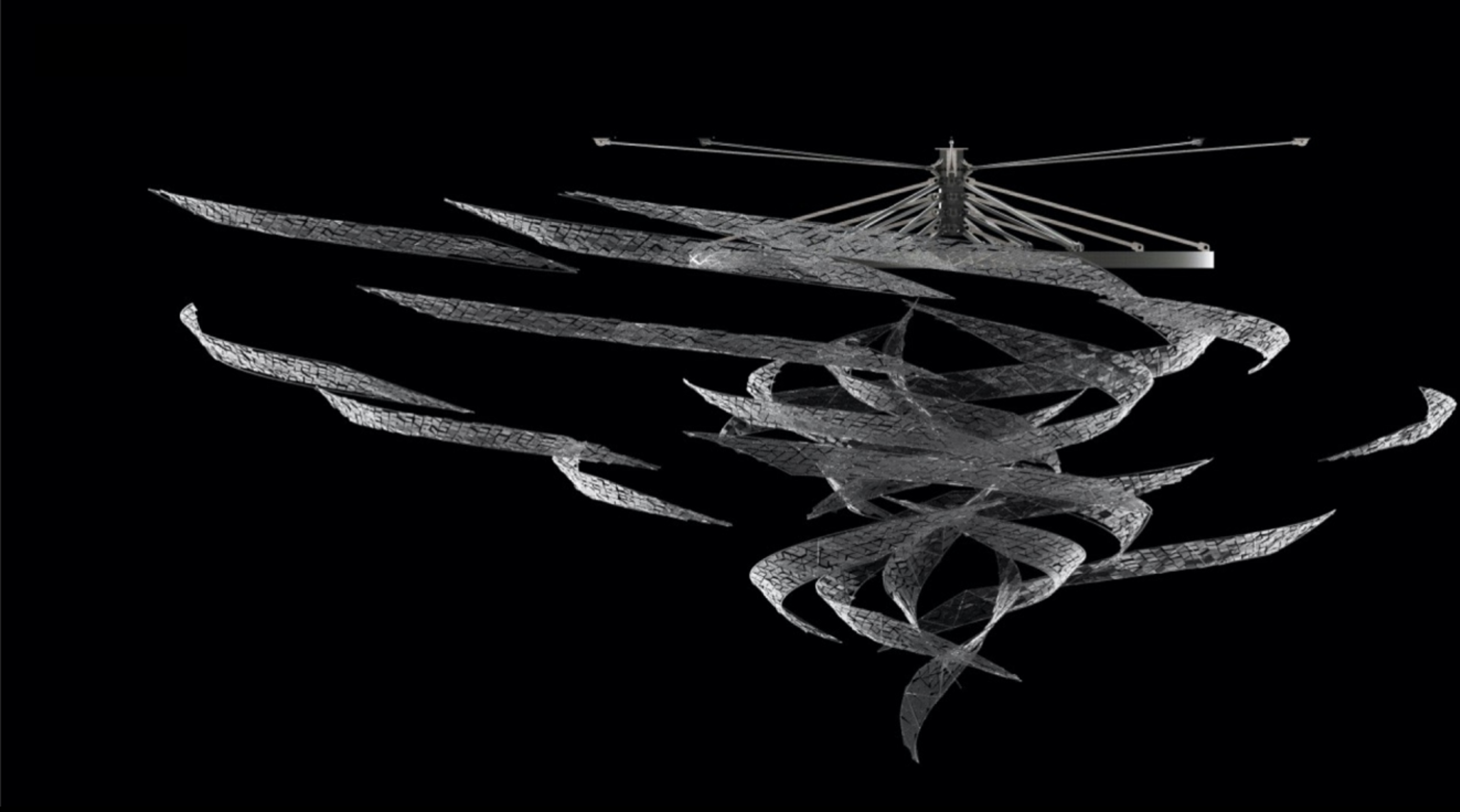
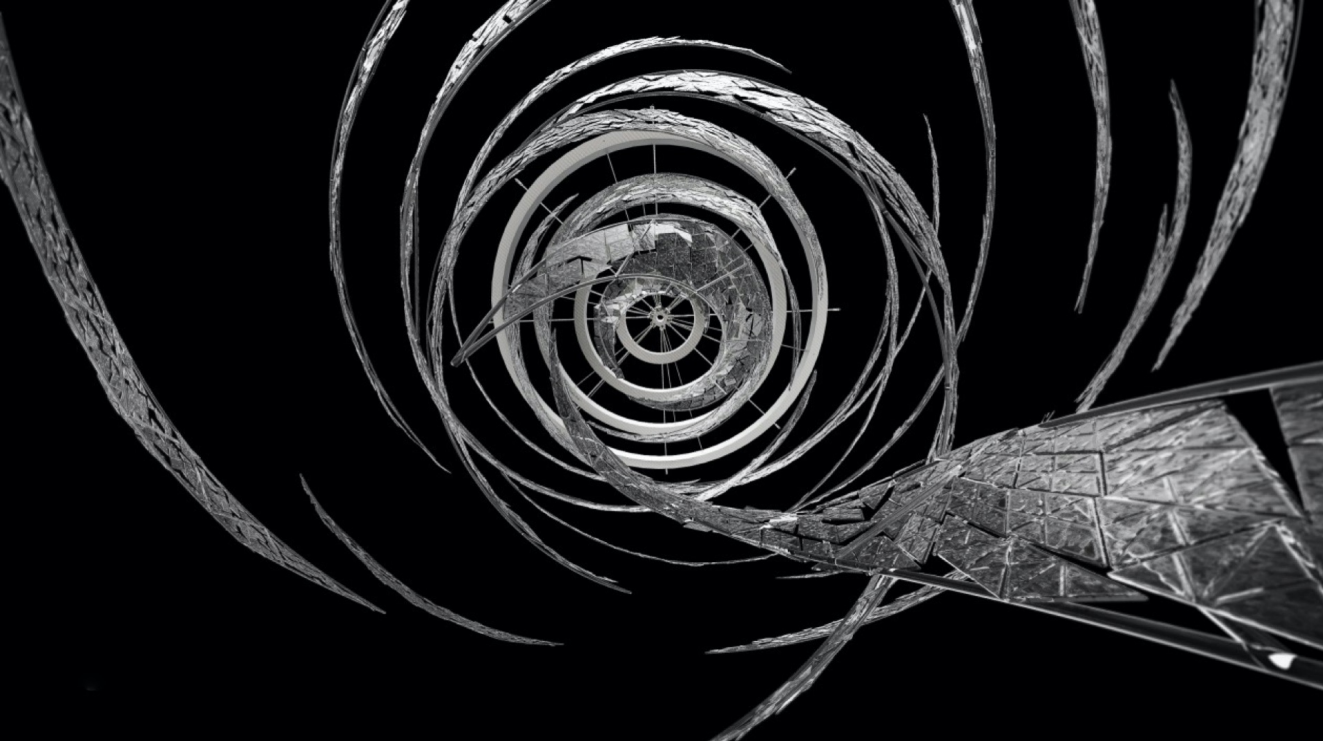
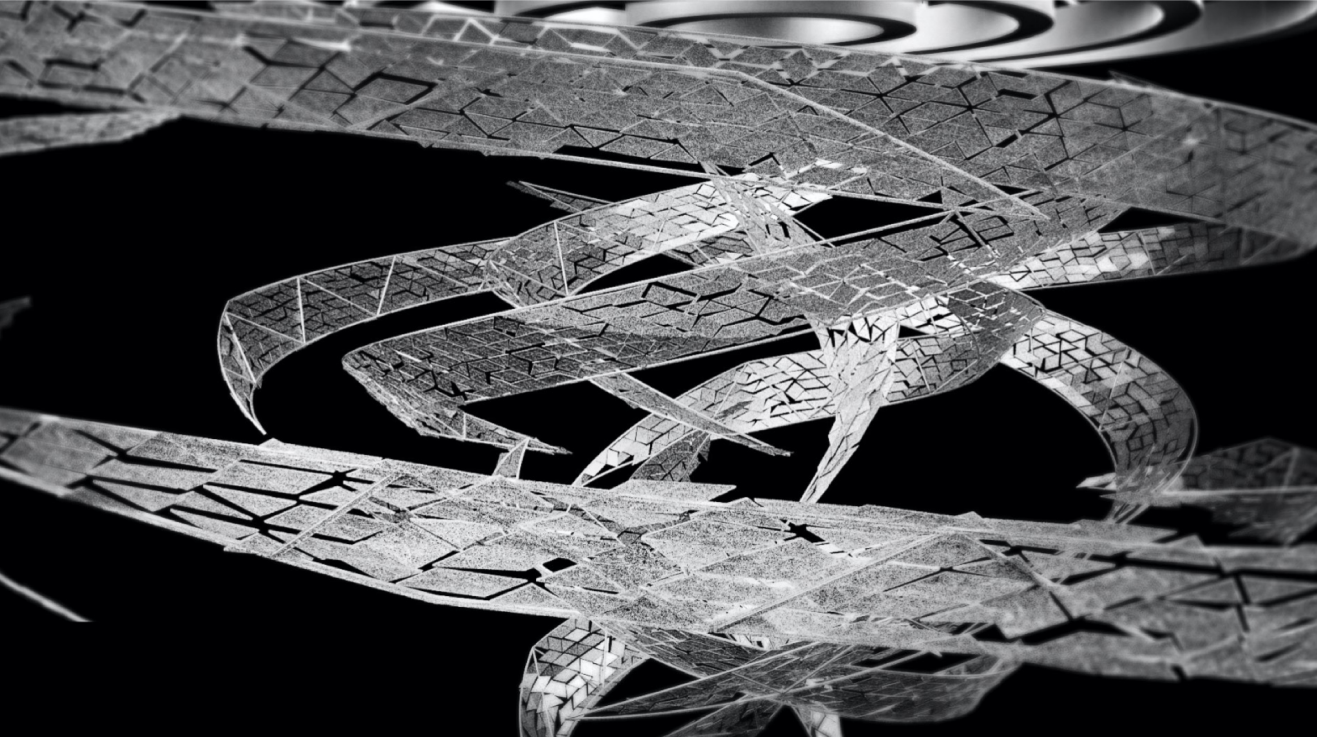
1.1 Notice
Once the concept and rendering of the product are developed, the question becomes how to implement it. This lighting fixture involves a variety of disciplines such as load-bearing, high-voltage and low-voltage electricity, GPS transmission, mechanics, thermodynamics, remote control, maintenance, and upgrades.
1.2 Weight
The lobby of Xi'an W is a pure steel structure, and the total weight of the initial model of the lighting fixture that we simulated was 17 tons, undoubtedly a mammoth. After careful calculation and reporting the weight to the owner, it was found that the on-site building could not meet this weight and required weight reduction.
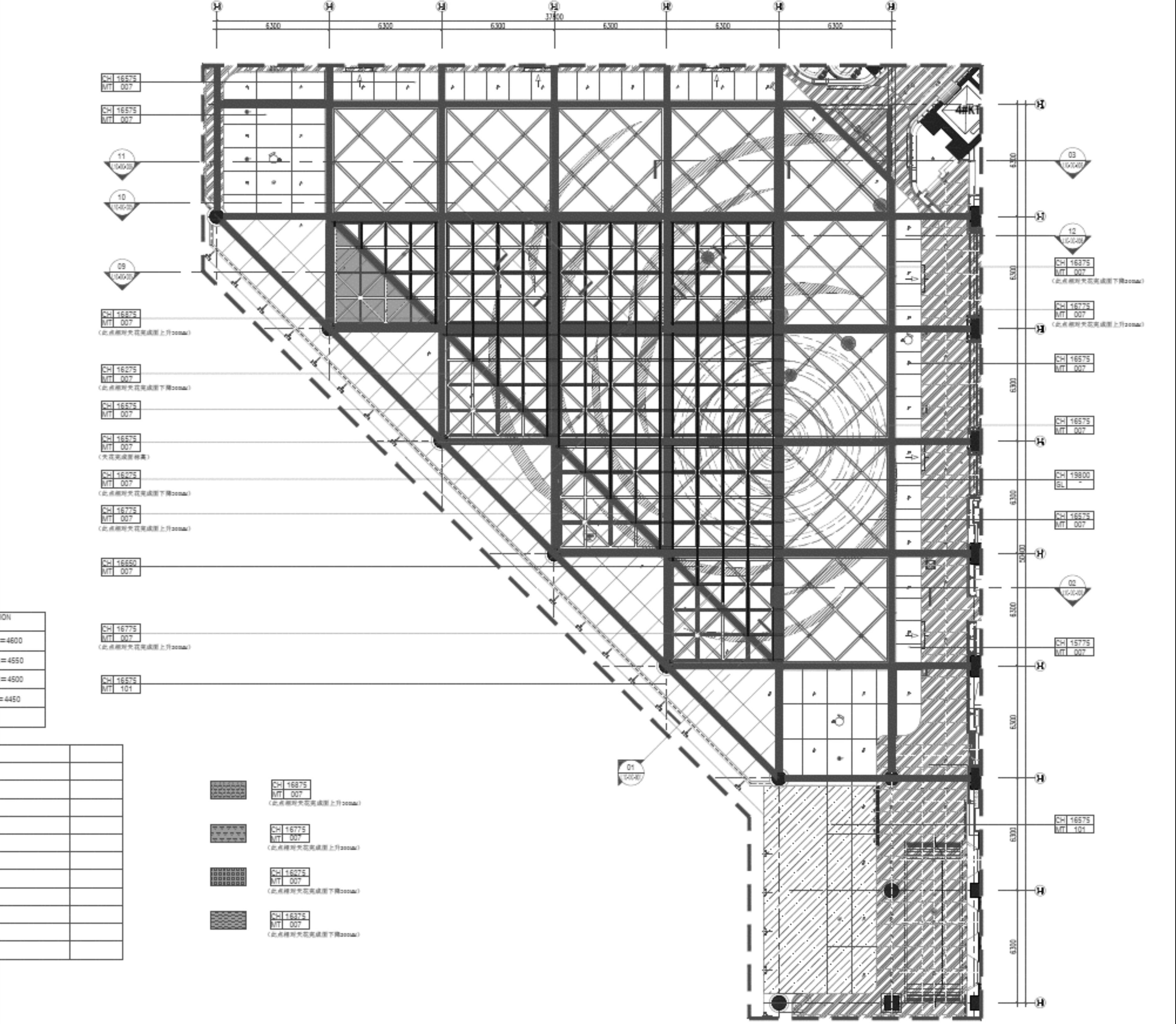
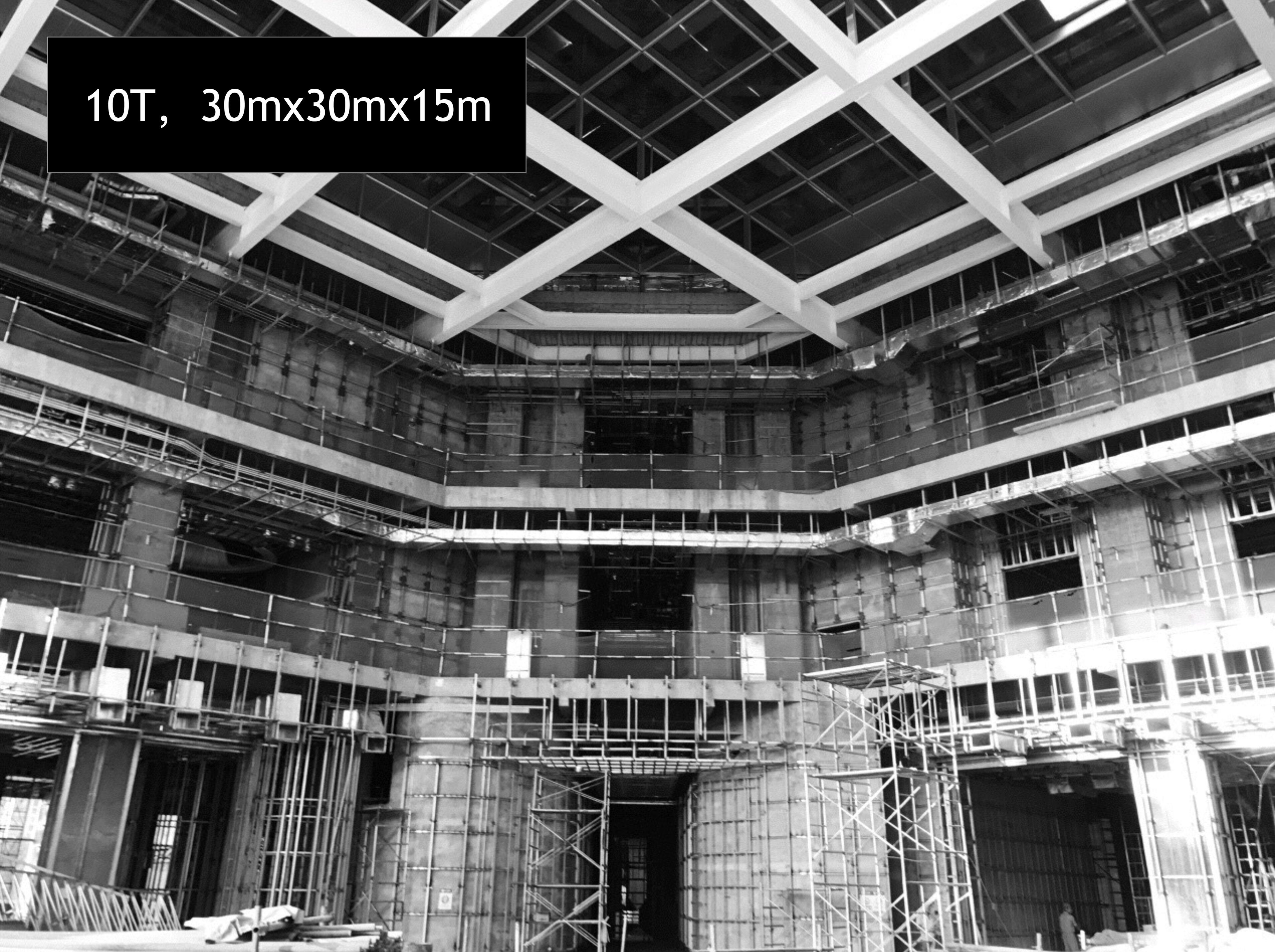
1.1.1 Site
The maximum load-bearing capacity of the building is 10 tons, and the size of 30m x 30m x 15m presents a huge challenge in terms of weight reduction while ensuring safety and rotation. Later, we tried various frame solutions such as laser-cutting a single sheet of metal, but they were all rejected due to failing to meet the weight requirements.
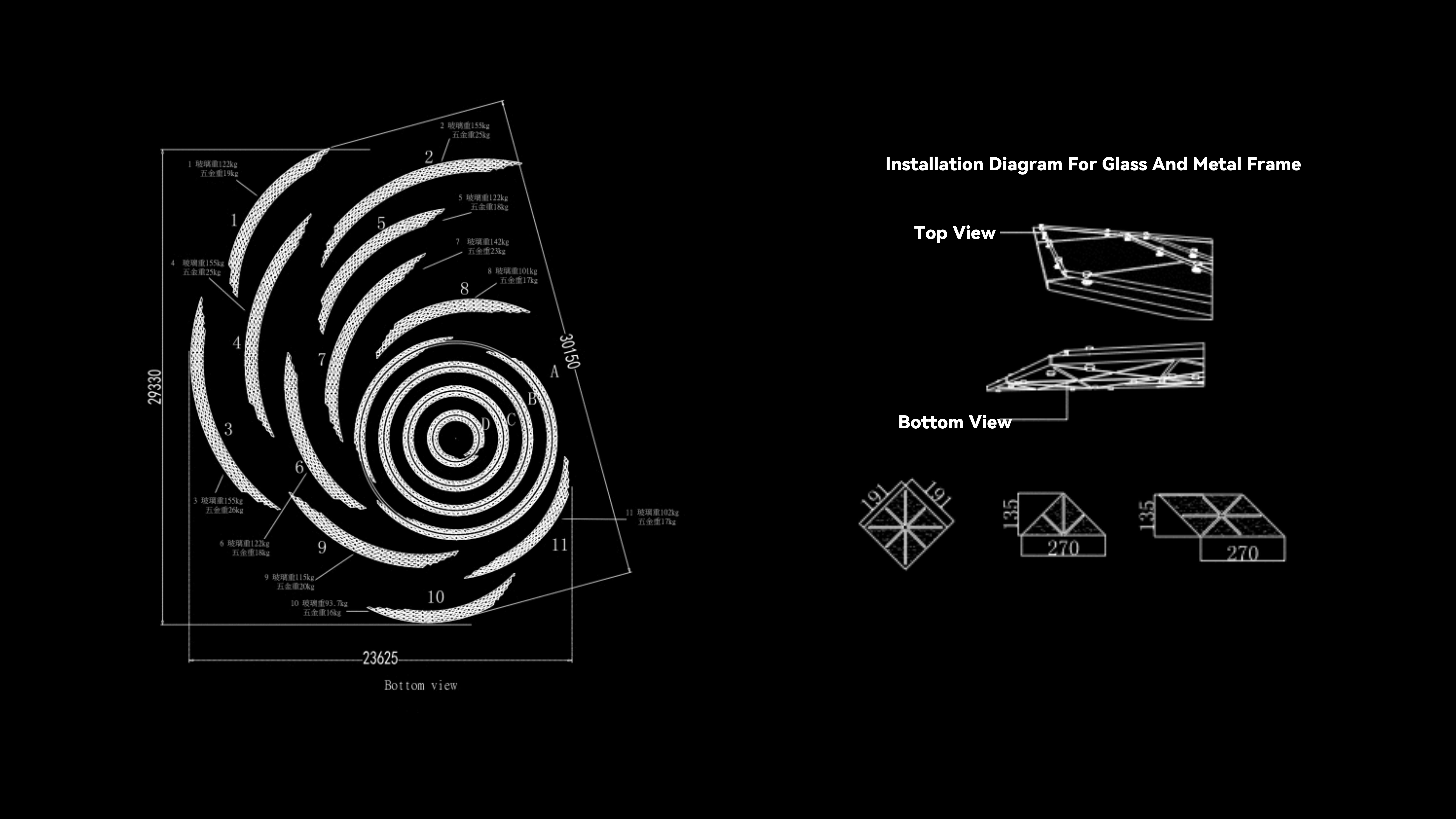
1.3 Soft Structure
In the end, we adopted a 304 stainless steel flexible structure to achieve the effect in the rendering, which was verified through theoretical and practical testing. This solution is closest to the effect of a crystal hanging in the air. At the same time, it reached a good balance critical point in terms of weight and load-bearing capacity. We sought the help of the mechanical engineering team at Dalian University of Technology to conduct an overall calculation of the load-bearing capacity, stress, and other mechanical and structural aspects. We went through dozens of calculations and verifications regarding the calculation of the load-bearing capacity, and finally succeeded in weight reduction through theoretical and practical tests.
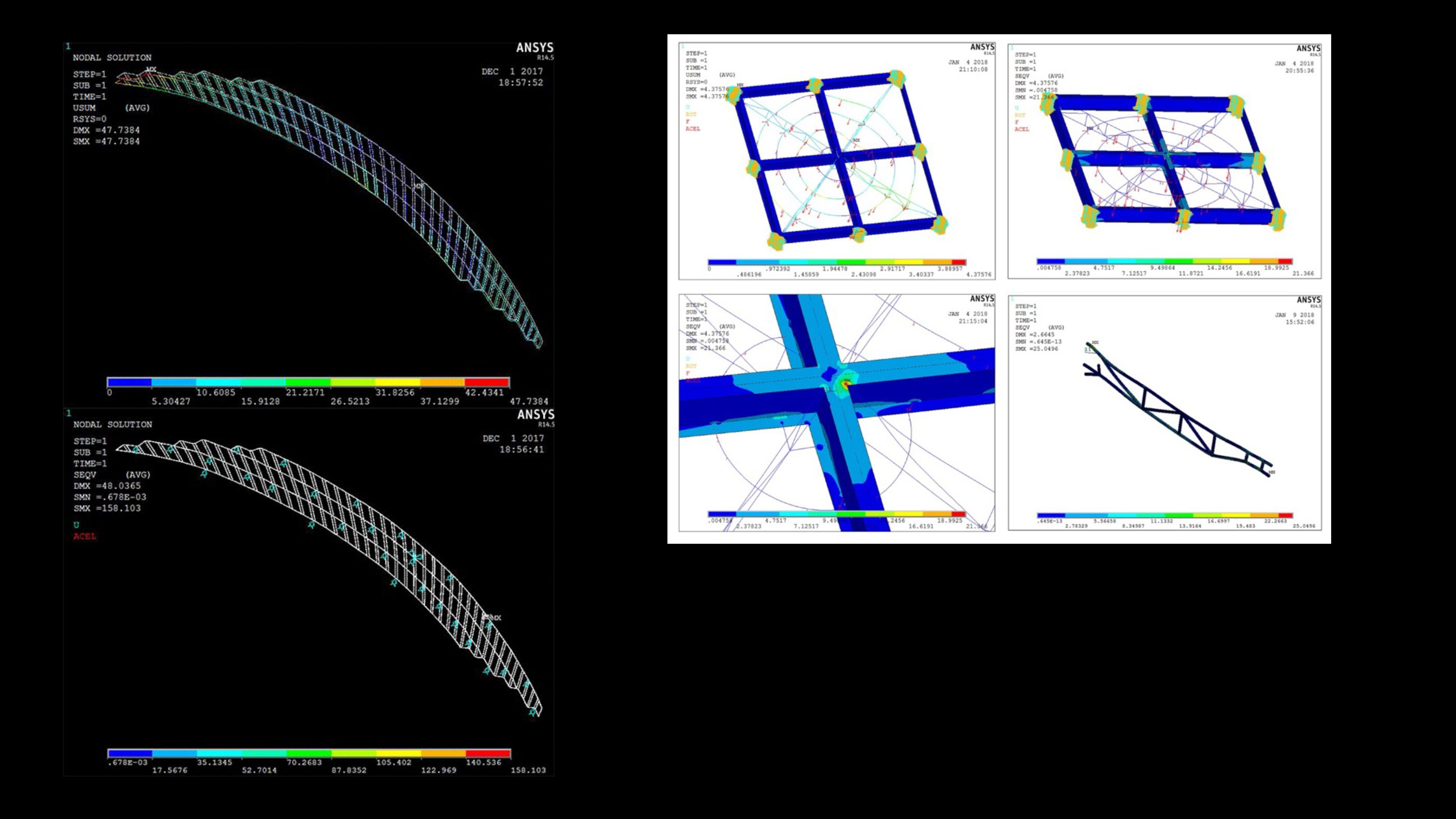
In this solution, how to reduce weight while ensuring safety is still the first major challenge we faced - the crystal must be as light and thin as possible while maintaining safety. Meanwhile, shaping and processing stainless steel material into a hyperbolic curve also posed a huge challenge. In the early stages, we conducted several tests on the frame and crystal, but the results were not ideal - the turning angle was not flexible enough, and the crystal effect was not transparent enough. However, after continuous simulation and correction, we finally found the best solution to achieve a smooth curve.
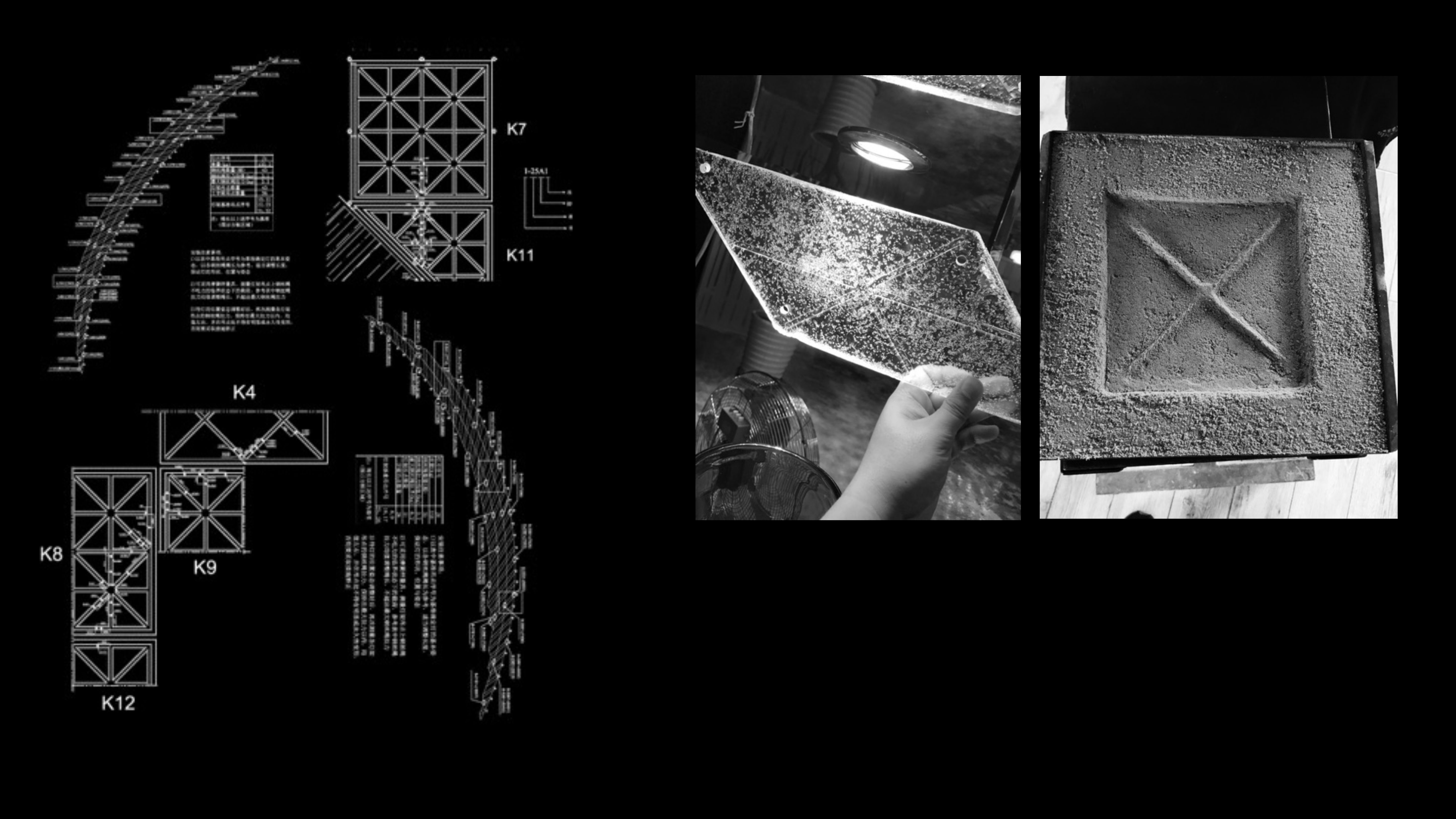
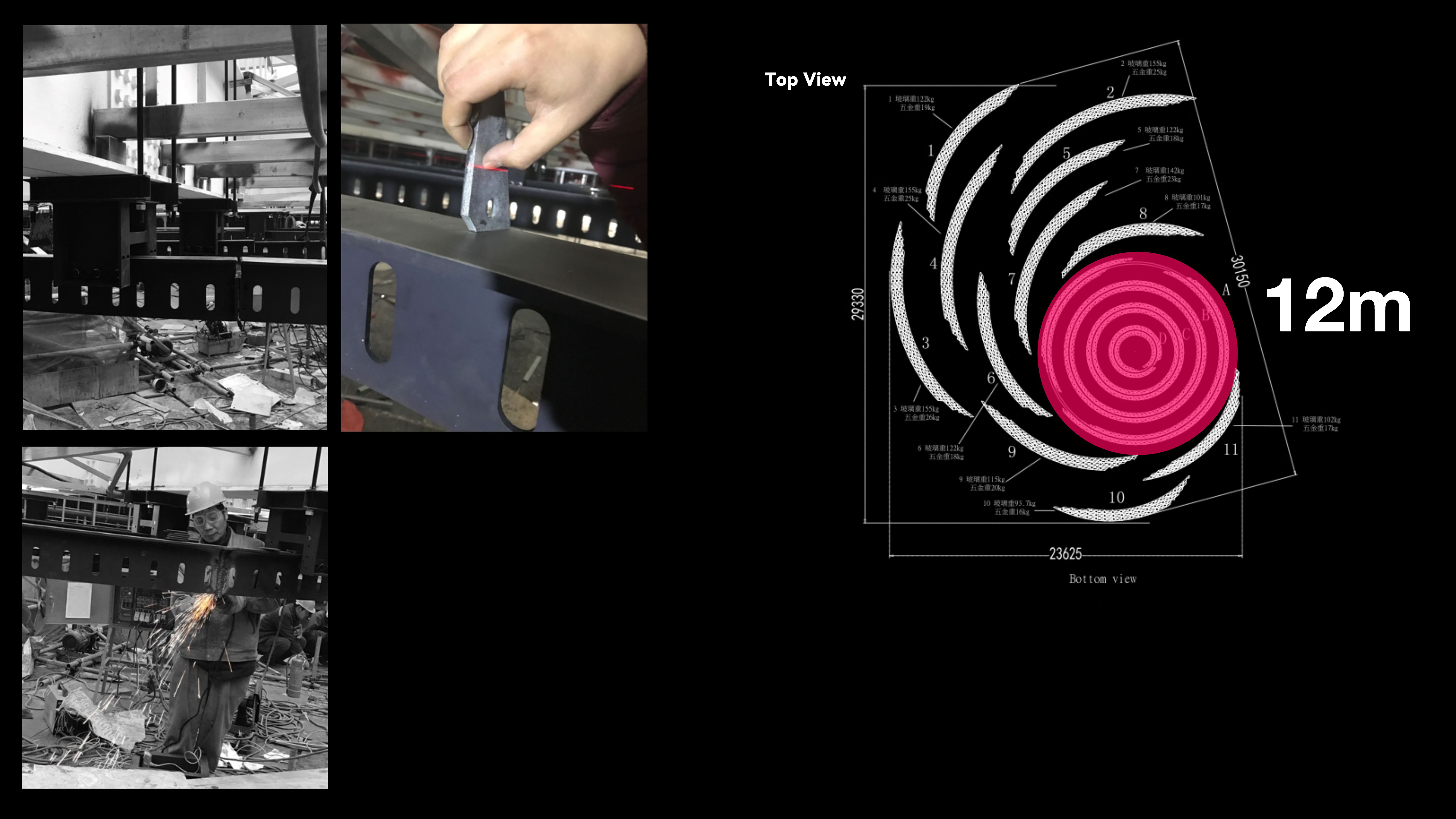
1.4 Track and Transportation
Due to the rigid requirement of load-bearing capacity, the diameter of the rail had to reach the maximum load-bearing capacity while the weight needed to be reduced to the lowest possible level. To reduce weight, we chose to shrink the cross-section of the rail and add weight-reducing holes on it. After production was completed, the rail had a diameter of 12 meters, making transportation a challenge whether by logistics or high-speed transport. In the end, we cut the rail into four parts for transportation and welded them on-site. After a week of trial operation of the rail, we began the installation process.
2 Grant Banquet Hall
The grand banquet hall's design concept is inspired by nature, featuring stunning crystal chandeliers that create a captivating ambiance and dynamic RGBW lighting scenes that add an eye-catching glow.
We worked closely with a design company to explore various styles and ideas, utilizing software to simulate the space of the grant banquet hall and produce a photorealistic 1:1 rendering of the final product.
1.6 Construction
We spent a whole year implementing the construction of the lobby, incorporating over 7,000 crystal pieces and more than 1,000 suspension points into the overall design.
1.5 Lighting and Power Supply
The crystal lighting fixture in the lobby requires RGBW color-changing and dimming. However, due to the rotation and curvature of the fixture, we were unable to achieve the optimal effect after trying multiple solutions. Finally, we drew on the experience of historical engineering and used wall washers to brighten and even out the crystal.
However, how to supply power to the dynamic area became another challenge. In order to meet the requirement of rotation, we first tried using cables. However, the cable could not rotate continuously, posing a safety hazard. Therefore, we decided to use a conductive slip ring. After several tests, we found the right slip ring that met our requirements.
In addition, we also installed an emergency power supply system to ensure that the lighting fixture could still operate normally in case of a power outage.
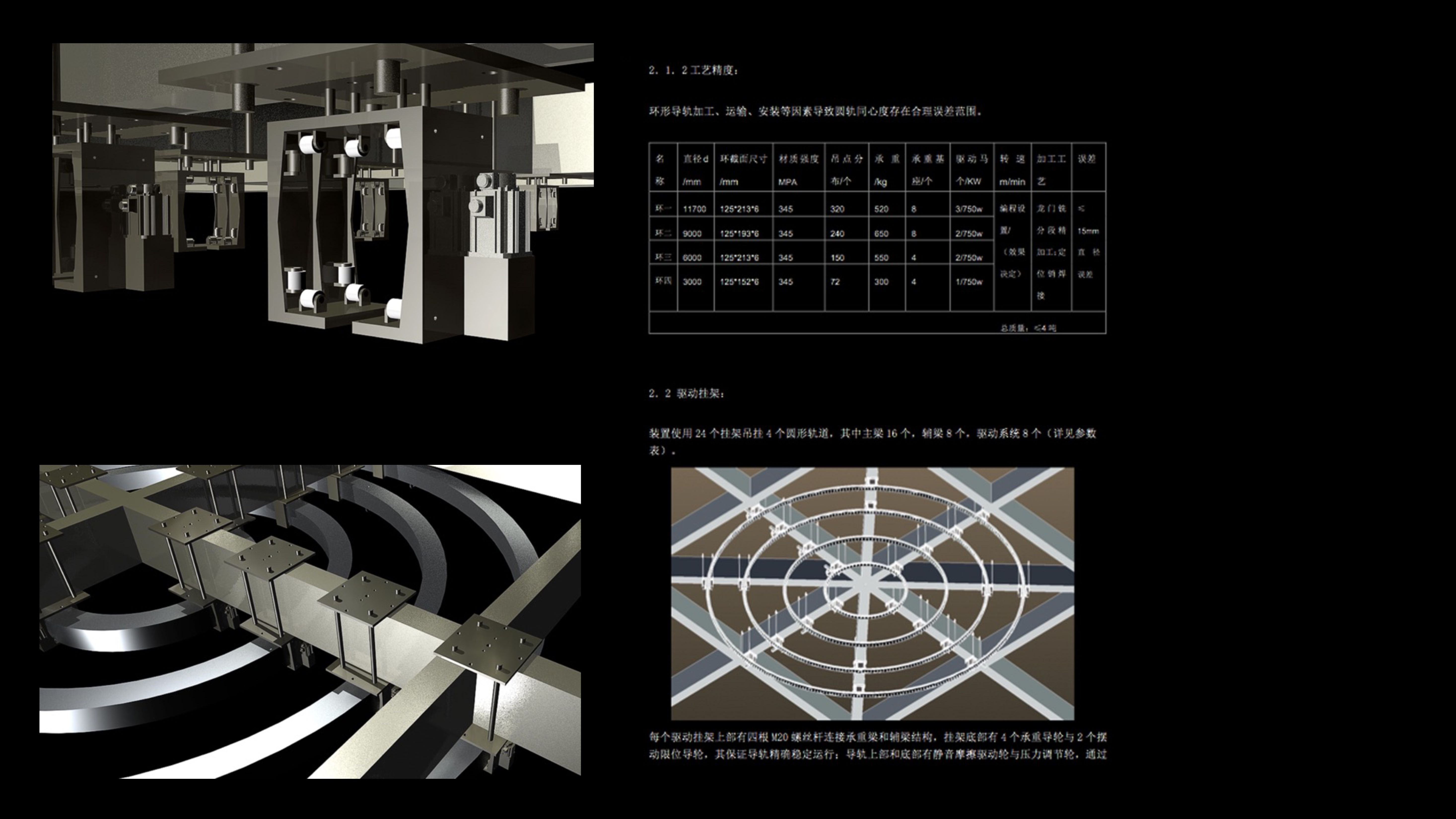
3 Small Banquet Hall
The curved design of the interface shape for the W Hotel and Wanzhong Real Estate (Wanzhong) was chosen as the first letters of their names in English, creating a striking visual effect. As a lighting fixture, the black keys do not emit light, while the white keys have RGBW color-changing capabilities. The entire ceiling of the small banquet hall is designed with black and white interlocking piano keys, which is both intricate in detail and stunning in overall design.
2.1 Acoustics Problem
The Grand Ballroom covers an area of 1500 square meters, and the use of large stainless steel material on the ceiling causes serious echo problems in actual use. To reduce the echo, we consulted with an acoustics professor from Tsinghua University to solve the ceiling acoustic problem. To soundproof, we added 2 million sound-absorbing holes to the ceiling panel. For the cutting tools, we used a German laser cutting machine to ensure that there were no residues after cutting and to achieve an ideal smooth surface.
The design, production, and installation of the Westin W Hotel's crystal chandelier is now complete.
4 Other areas
Chinese restaurant/ Presidential suite
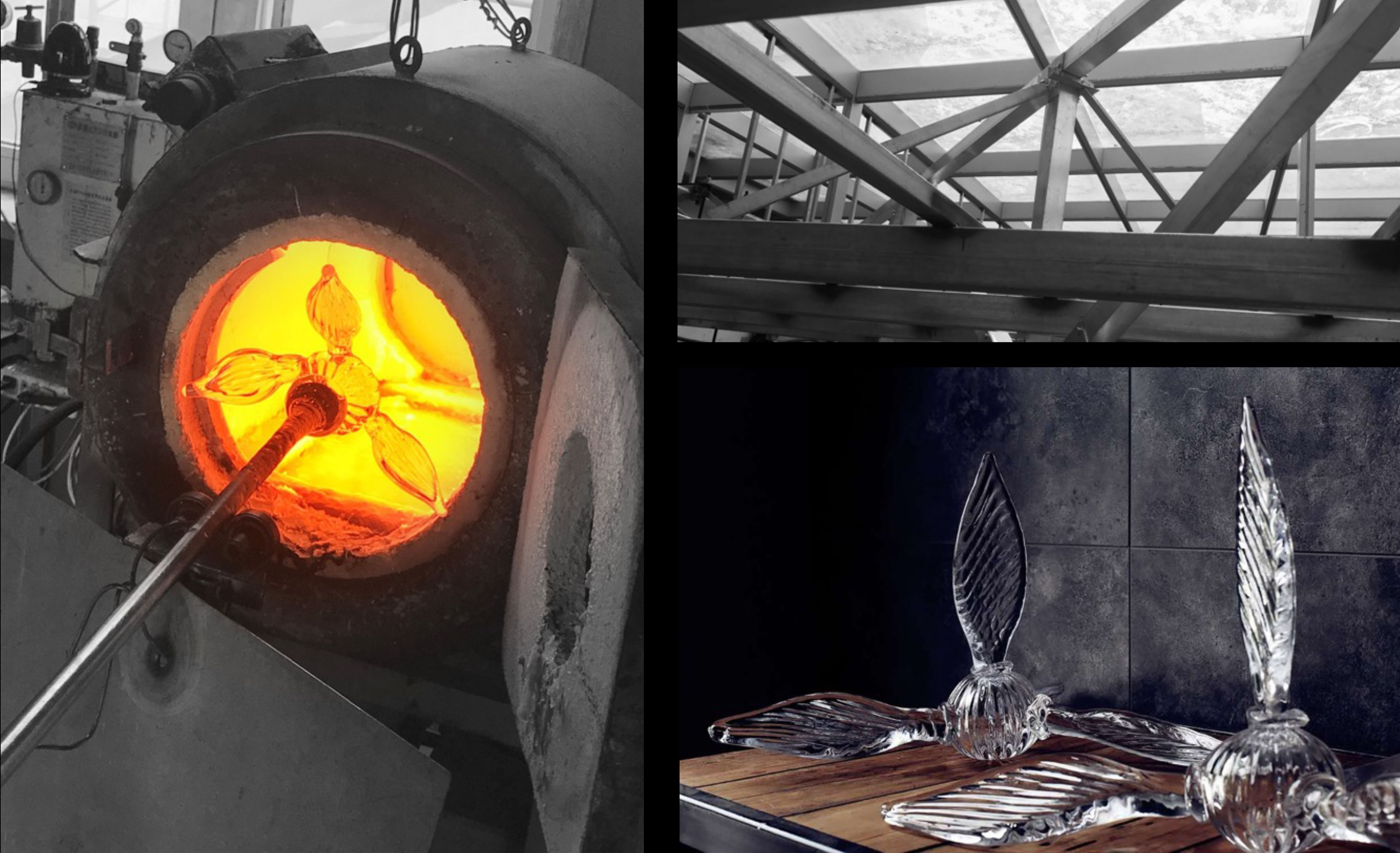
2.2 Load-bearing Maintenance & Testing
For later maintenance, we separately constructed a 1500 square meter load-bearing conversion layer. We built an air floor above all the lighting fixtures in the Grand Ballroom to ensure the convenience of upgrading and replacing accessories. All crystal lamps were hand-blown. During the production of the crystal samples, we continuously tested the on-site sound vibration and lifting safety and continuously improved the process and production sequence to meet the on-site safety requirements. At the same time, we specially developed a hot-melt adhesive process to adapt to the lifting safety requirements of the Grand Ballroom.
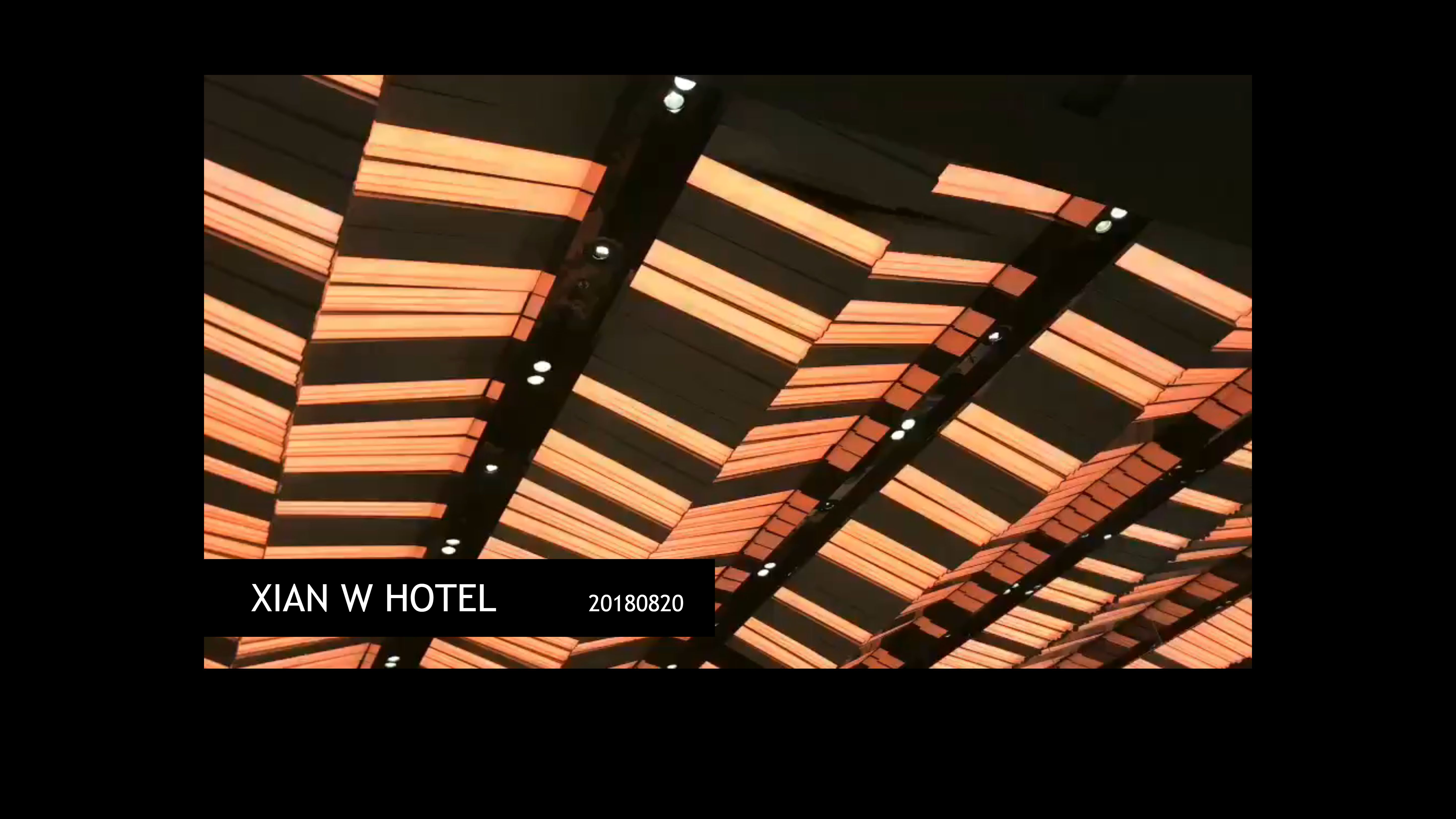
2.3 Rehearsal & Construction
The installation workers have undergone systematic and comprehensive training and are familiar with the lifting sequence. The entire chandelier requires the installation of 3525 horses, each with a lamp wire, and is fixed and adjusted by three steel wires. There are 14,100 points on the construction site, like a meticulously arranged surgery, requiring close cooperation between installation personnel and system engineers. After more than a month of construction and adjustment, the hardware installation of the Grand Ballroom banquet lamps was completed.
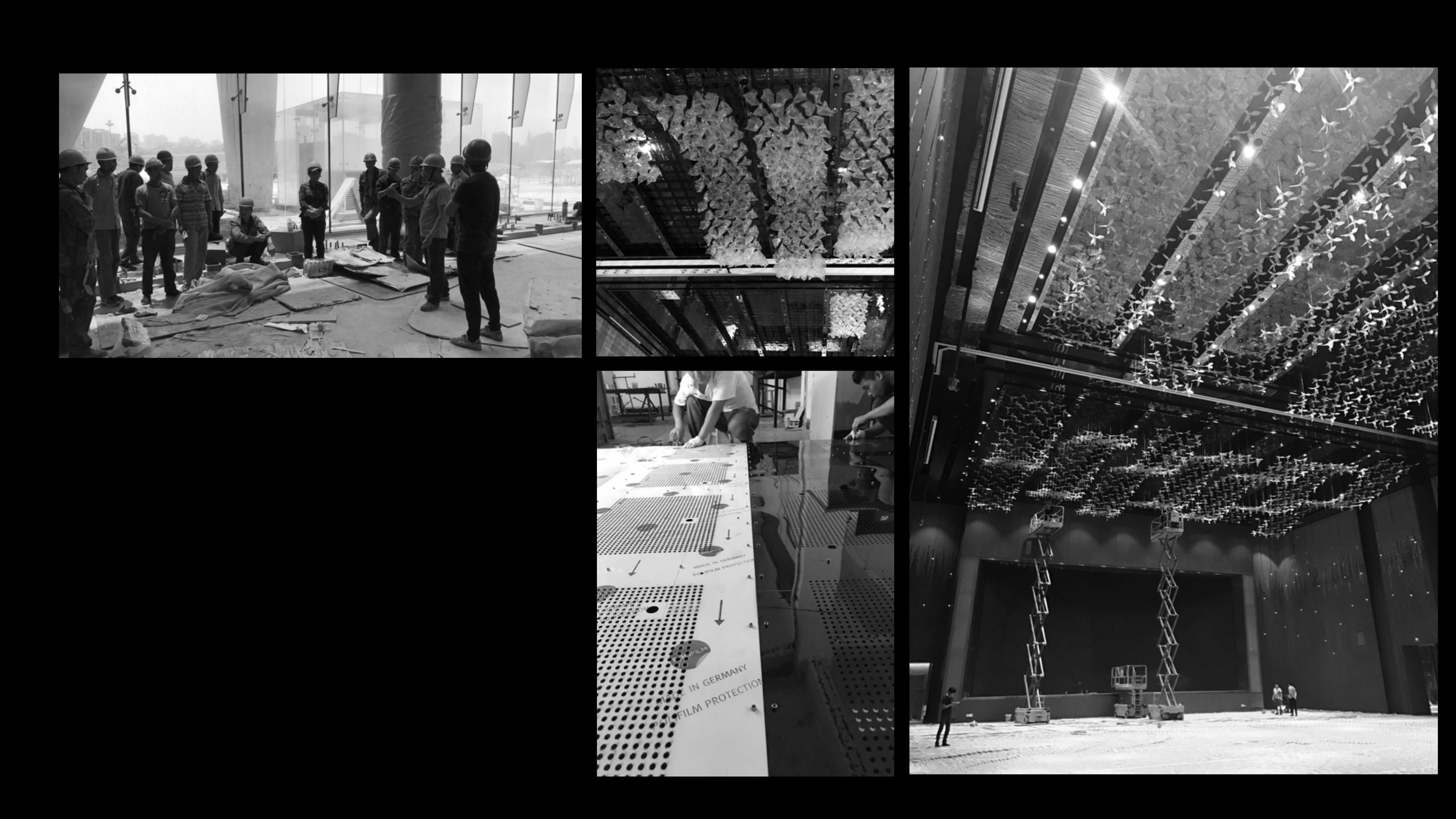
2.4 Programming
Our lighting design is all preset in advance. Finally, the programming engineer came to the scene to adjust and reprogram the existing program according to the on-site environment to achieve the most ideal lighting effect.
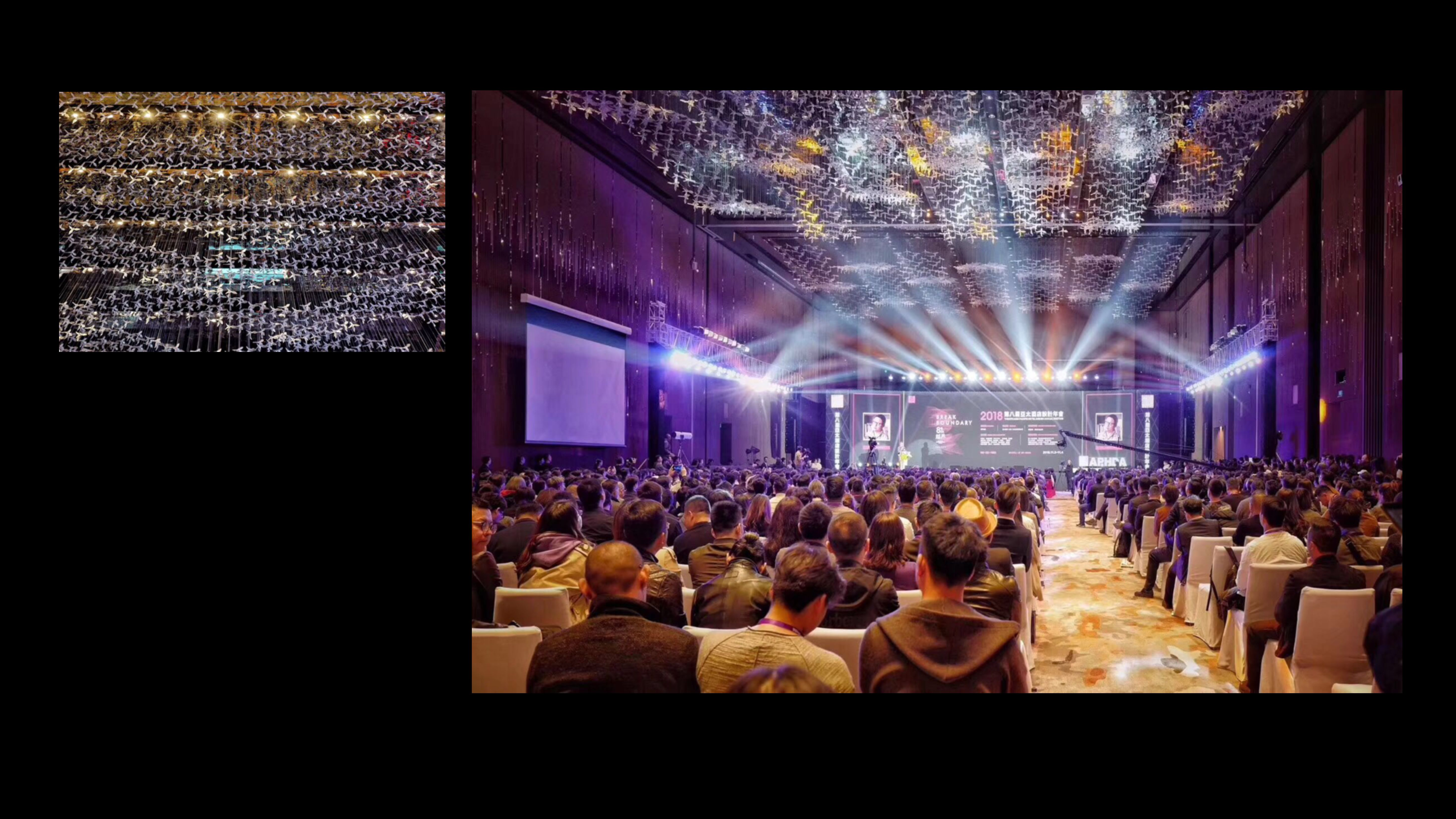
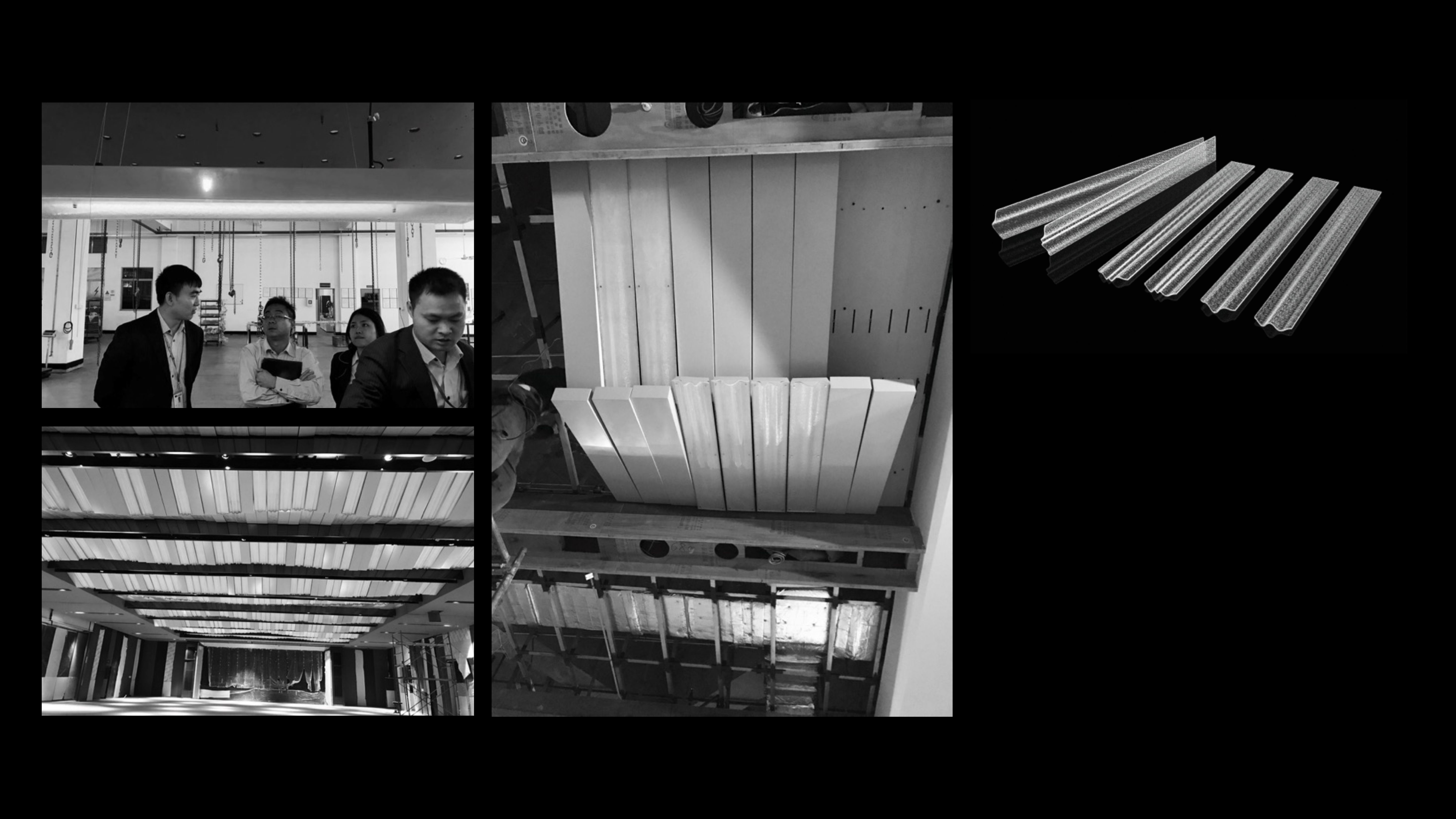
3.1 Technical Experimentation
To achieve this shape, we continuously attempted to break through past technological bottlenecks to achieve the ultimate results in transparency and curvature. We also put a lot of effort into the lighting design of the illuminated piano keys. Due to the large size of the piano keys, we chose a four-point suspension method for installation. At the same time, due to the inevitable dimensional errors in the hard installation process, we had to carefully consider how to fix the positions of the piano keys and ensure appropriate adjustability in the early design stage.
3.2 Programming
Considering that the piano keys cannot emit scattered light during actual use by customers, we simulated normal dining mode, meeting mode, and party mode for dimming intensity, with each effect and programming prioritizing user experience and aesthetic appeal. After a week of fine-tuning, we delivered a perfect product.
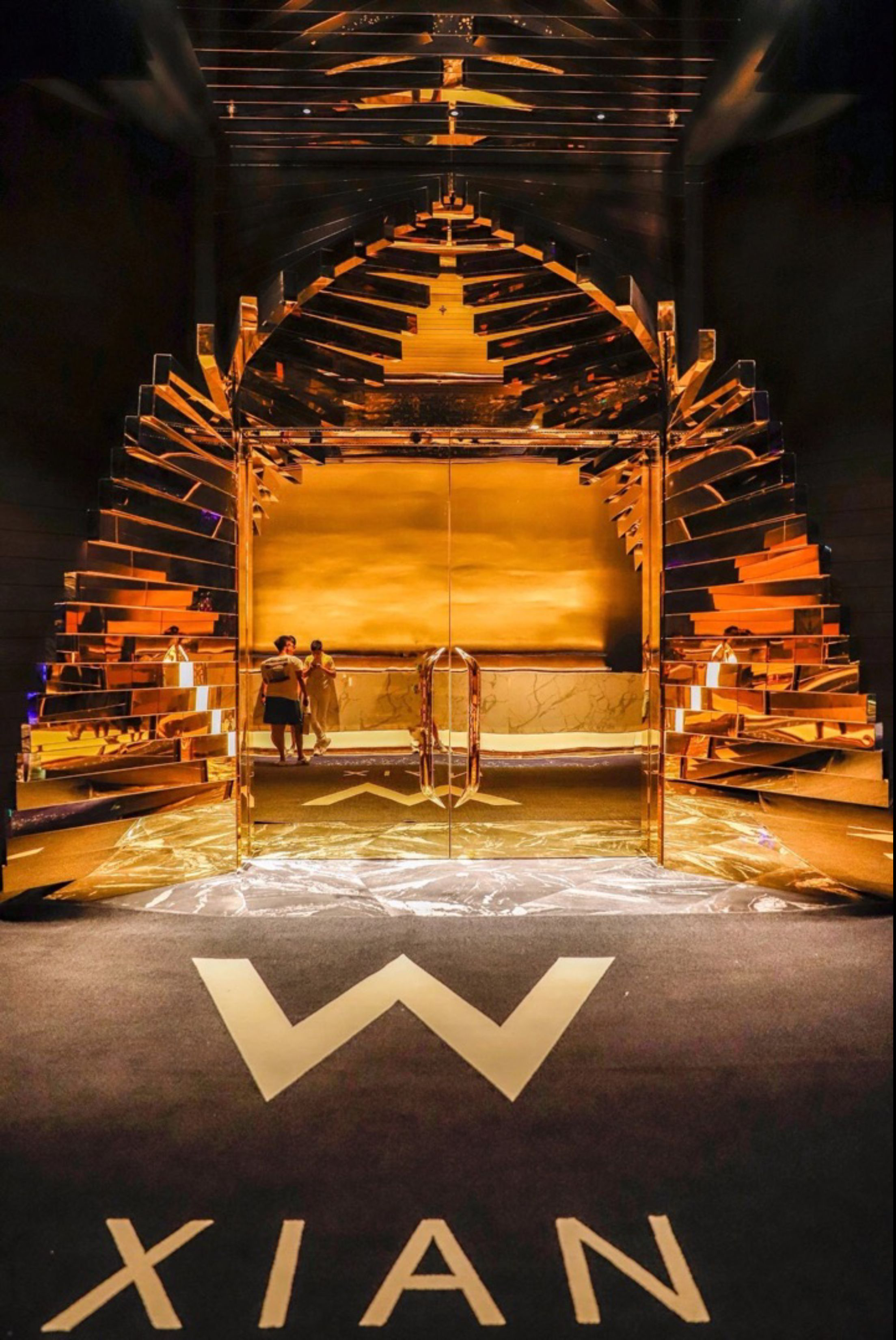
Post time: Mar-22-2023